Bellway and Nuspan test energy and cost-efficiency of precast floor in The Future Home
Bellway has partnered with Nuspan Flooring to assess the impact that precast floors may have on a new home's energy efficiency and cost of living as part of its new Future Home project.
Nuspan has installed the structural insulated closed floor panels, which are manufactured off-site, within The Future Home at Energy House 2.0. This is an important component of the ongoing research project taking place at the University of Salford which is dedicated to improving the sustainability of new homes.
Bellway is positioning itself as a pioneer in sustainability within the construction industry by taking part in this project. Therefore, the results of these tests are crucial to the project's success and shapes the business’s future operations.
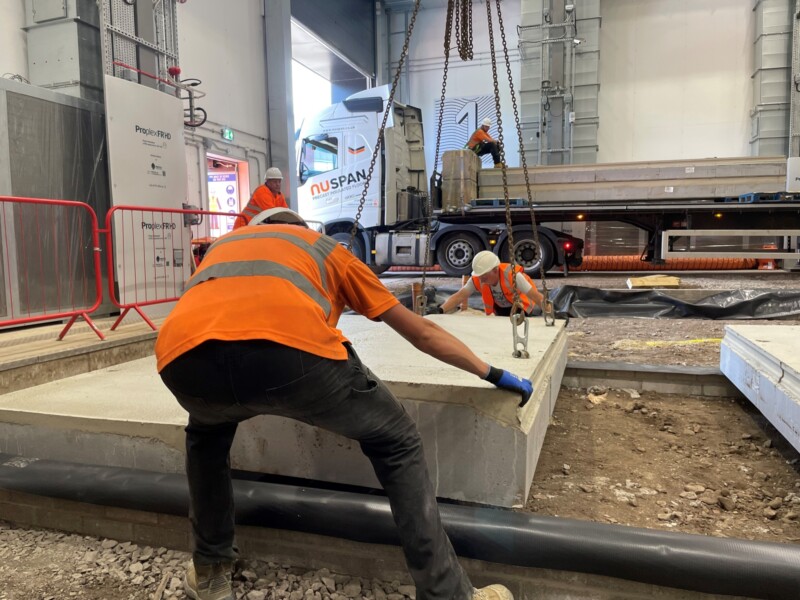
“Energy House 2.0 has the potential to change the way new homes are built by examining every aspect of the fabric and monitoring its efficiency. Nuspan’s input will give us a better understanding of the advantages insulated precast flooring could offer.”
Jamie Bursnell, Group Technical and Innovations Manager for Bellway, said: “The Future Home at Energy House 2.0 will enable us to analyse the real impact each individual aspect of the building fabric has on a home.
“The Nuspan floor within the home will work alongside underfloor heating. We chose Nuspan as a partner because the company is a market leader in off-site flooring manufacture. Its commitment to reducing waste and energy usage aligns both with this project and with our Better with Bellway sustainability strategy.
“The installation of the floor demonstrated the advantages of off-site manufacture. Delivering a completed unit to be fitted at the site meant fewer tradespeople were required to visit. The floor was ready to walk on immediately, which enabled us to press ahead with the next stage of build more quickly.
“Energy House 2.0 has the potential to change the way new homes are built by examining every aspect of the fabric and monitoring its efficiency. Nuspan’s input will give us a better understanding of the advantages insulated precast flooring could offer.”
Helen Wildin, Sales and Marketing Manager for Nuspan, said: “We’re proud to be working with developers, helping them to meet their commitment to net-zero carbon emissions by 2050. We try to achieve this by running a circular economy in our factory, leaving no material waste on site, and achieving U-values as low as 0.10 W/m²K on ground floors.
“It has been a privilege to partner with Bellway on Energy House 2.0. This is a game-changing research and development project for the industry, so we’re looking forward to seeing how the results shape the future of housebuilding.”
When compared to conventional ground floor construction techniques, Nuspan has many advantages. Nuspan was created to comply with the next generation of building rules. This allows the building designer greater flexibility when specifying other elements of the building in order to achieve the required Target Emissions Rating (TER) or to achieve highly energy efficient buildings.
For these reasons, there is a lot of optimism that this partnership will be very successful for the project and help to pave the way for more sustainable homes.
The Energy House 2.0 project is being part-funded by the England European Regional Development Fund as part of the European Structural and Investment Funds Growth Programme 2014-2020.
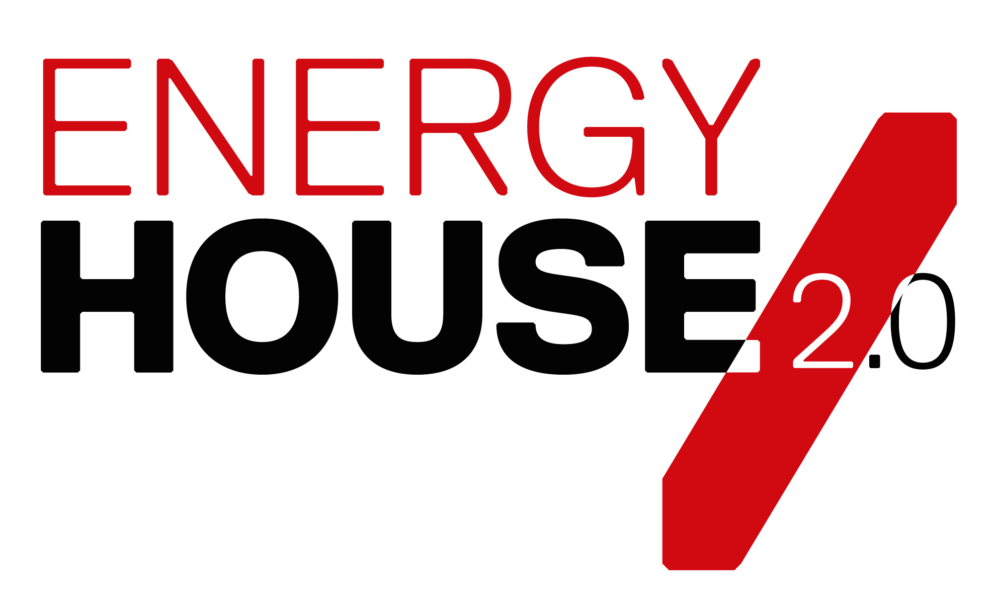

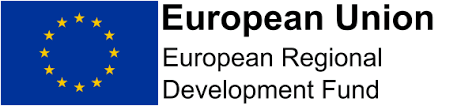